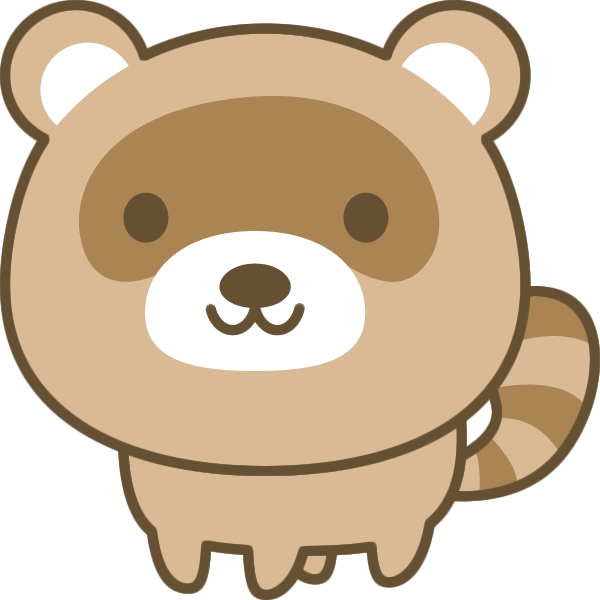
化学プラントではDCSっていうシステムで工場の運転を監視・制御しているらしいんだけど、どのようなものなんだろう。
本記事では、現在化学工場を運転するのには欠かせない存在になっているDCSに関して解説していきたいと思います。
DCS(分散制御システム)とは?
DCS(Distributed Control System)は分散制御システムと呼ばれ、主に産業のプロセス制御や製造ラインにおいて、複雑な制御操作を分散型で行うためのシステムです。
DCSは、複数の制御装置(コントローラ)がネットワークで接続され、各装置が一部の機能やプロセスを担当することで、全体のシステムを効率的に運用します。
例えば、石油化学プラントや製薬工場など、大規模かつ複雑な生産プロセスを持つ現場において、その強みを発揮します。
DCSのシステム構成
DCS(分散制御システム)のシステム構成は、その名の通り、制御機能を分散して配置し、全体で一元的に管理・制御を行う仕組みです。
一つのシステムの中に複数の機能があるのではなく、複数の製品や設備を連携するためそれぞれの区分(ユニット)ごとに制御機器が設置されています。このように制御ユニットを分けることで、万が一どこかのユニットに不具合が発生してもシステム全体が止まらない・トラブルが波及しないことから、長期継続運転が可能な仕様になります。リスクの分散だけでなく、設置場所や機能そのものの分散も含まれます。
DCSは、複雑なプロセスや設備の制御に適したシステムであり、その構成は一般的に以下の主要な要素から成り立っています。
1. コントローラ(Controller)
DCSの中心となる部分が「コントローラ」です。上の図でDCS盤と書いてある部分です。
コントローラは、各プロセスの制御を担当しますが、DCSではこれが複数台存在し、分散型のアーキテクチャを形成します。
コントローラは、各制御対象(例えば、温度、流量、圧力など)のデータを収集し、計算した制御指令を送信してプロセスを最適化します。
コントローラーの名称は各DCSメーカーによって異なり、DCS大手の横河電機ではFCS(Field Control Station)と呼ばれています。
2. 制御PC
次にDCSシステムの監視・操作を行うためのインターフェースとしての制御PCがあります。
オペレーターはここでシステム全体の状態を監視し、必要に応じて制御パラメータを変更したり、異常が発生した場合に対応を行います。
これも各種メーカーによって呼び方が異なっていたりします。
よく聞くところでいうと、HIS(Human Interface System)、MMI(Man Machine Interface)、HMI(Human machine Interface)あたりでしょうか。
どれも、意味としては同じ感じですね…
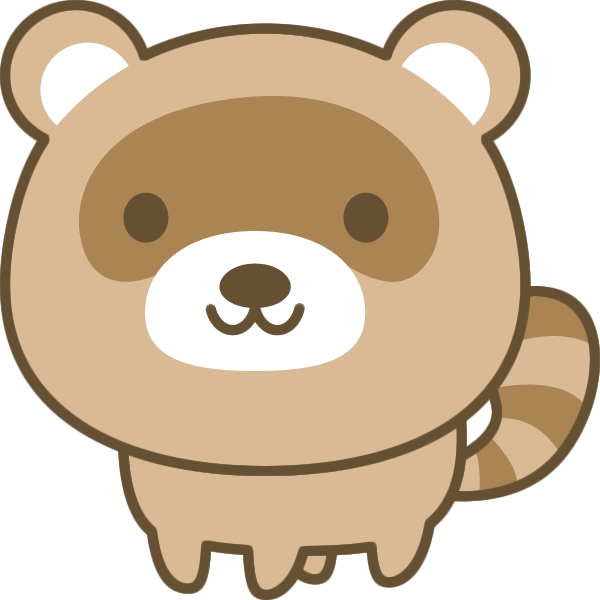
実際の運転ではこのPCの画面を見て工場全体の状態を監視するから、一番身近なところだね!
3. ネットワーク(Communication Network)
DCSは、分散型のシステムであるため、複数のコンポーネント(コントローラ、オペレーター・ステーション、I/Oモジュールなど)がネットワークを通じて連携します。
これは各社とも冗長性の高いネットワークシステムを採用しており、1つの通信経路に障害が発生した場合でも、別の経路でデータが転送されるようになっています。
DCSの特徴
DCSのシステムの特徴としては以下の特徴があります。
- 分散型構造
DCSは、複数のコントローラがシステム全体を分担して制御します。これにより、システム全体が一元管理されることなく、柔軟で冗長性のある制御が可能になります。万が一、1つのコントローラが故障しても、他のコントローラがシステムを維持できるため、高い可用性が確保されます。 - リアルタイム性と柔軟性
DCSは、リアルタイムでのデータ収集と制御を行う能力があり、プロセスの各段階で発生する変化に即座に対応します。また、システムの構築が比較的柔軟であり、将来的な拡張にも対応しやすいという特徴があります。 - 高度な監視・診断機能
DCSは、システムの監視機能や故障診断機能が強化されており、オペレーターが操作画面を通じて直感的にシステムの状態を把握できるようになっています。これにより、運用中の異常の早期発見と迅速な対応が可能になります。 - 制御の自由度
DCSでは内部でシーケンスを作成し実行することで弁の操作などのタイミングを自動で行うことができます。これにより工程ごとの操作などが簡単に実施することができ人為的ミスも減少させることができます。 - 高い拡張性
コントローラーや制御PCなどが複数分散してシステムが構築されているので、追加でコントローラーやPCを加えることが容易にできます。
そのため、能力増強などの工事の際も問題なく対応することができます。
DCS制御ループ
前述のDCSの特徴で制御の自由度が高いと記載しましたが、実際にどのような制御が使用されているかを簡単に紹介します。
- オート(AUT)制御
アナログ計器:PV値をSP値に制御するため自動でOP値を変更する制御
デジタル計器:シーケンスを用いて自動で動作させる制御 - マニュアル(MAN)制御
DCSから手動で操作をする制御 - フィードバック制御
主に流量や圧力制御に用いられ、検出端で測定した値を、操作端に送り一定の値を保つようにする制御。外乱に強く安定的な制御が可能 - フィードフォワード制御
先行動作と呼ばれ、熱プロセスやコンベアなどの外乱が大きい場合に使用する制御。フィードバック制御と合わせて使用し先に検出した外乱に合わせて制御する - シーケンス制御
あらかじめ決めた手順で進めていく制御 - 比率制御
複数の流体を一定の比率で混合するための制御 - カスケード制御
フィードバック制御系において、1つの計器の信号によってほかの計器に目標値を変化させて行う制御。
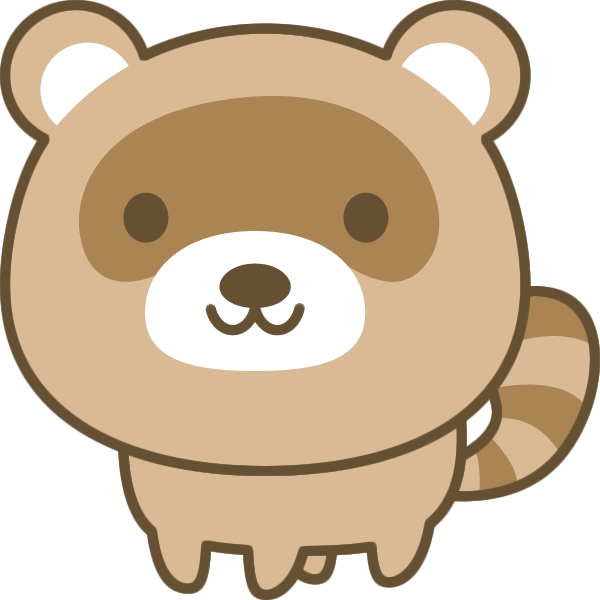
いろんな制御があるけど、フィードバック制御やオート制御が基本的に用いられている気がするよ!
DCSの制御に関してはまたまとめて紹介したいと思います。
PLCとの違い
DCSと似たものとしてPLC(プログラマブル・ロジック・コントローラ)があります。
これらはいずれも制御システムとして用いられますが、その用途や構造において以下のようないくつかの重要な違いがあります。
- 用途の違い
PLCは主に、機械的な設備の制御や単純なオン・オフ制御、タイミング制御などに用いられます。対して、DCSは、複雑なプロセス制御を必要とする場面、例えば温度・圧力・流量などを連携して制御するシステムに適しています。DCSは、通常、連続的で高度なプロセス制御に特化しているため、より大規模で複雑なシステムに向いています。 - システム構造
PLCは基本的に、1つのコントローラがシステム全体を制御する構造を取ります。これに対して、DCSは分散型の構造を採用しており、各制御装置がシステム全体の一部分を管理します。この分散型のアーキテクチャにより、DCSはシステム全体の冗長性と可用性を確保することができます。 - スケーラビリティと柔軟性
DCSはスケーラビリティに優れており、必要に応じてシステムを拡張しやすいのが特徴です。大規模なプロセスで使用されることが多いため、コントローラの数や機器の数が多くても、適切に管理できます。対して、PLCはシンプルな構造で小規模から中規模のシステムに適しており、大規模なシステムに対してはDCSほどの柔軟性を持ちません。 - データの集約と監視
DCSは複数のコントローラが相互に連携してデータを集約し、全体の制御を行います。これにより、プロセス全体のデータを一元的に管理し、最適な制御が可能となります。PLCは、通常は個別の制御装置として動作するため、システム全体の監視機能はDCSに比べると劣る場合があります。
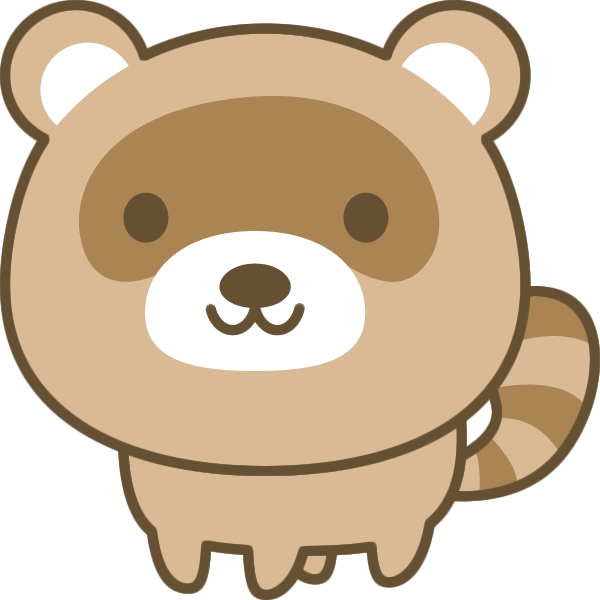
最近ではPLCでもある程度大規模なシステムでも構築できるようになってきて便利になってきていると感じるよ。
まとめ
DCSは、分散型制御しており、プロセス産業などでの高い可用性と柔軟性を備えたシステムになります。
PLCと比較すると、DCSは複雑なプロセスを一元的に管理し、冗長性や可用性の確保を重視したシステムです。
DCSは大規模なプラントでは欠かすことのできないシステムとなっていますので、皆さんもDCSについての理解を深めていただけると幸いです。
コメント